Ever wondered how acoustic guitars are made? While they might appear a simple instrument on first impression, there’s a lot of history, ingenuity, and expertise that goes into producing a quality acoustic guitar, far more than an electric guitar. In the following article, we’re going to take an in-depth look at the entire process.
Acoustic guitars are made by sourcing the materials (tonewoods), shaping, marking out the soundhole, planing and thicknessing the top (soundboard), and installing bracing to handle the tension from the strings and distribute vibrations. The back and sides are then cut to shape. The back is also braced, and linings are installed on the sides of the body to increase the surface area for gluing the top and back. The neck is then built, using a scarf joint to connect the neck to the headstock. The fretboard is constructed next and calculations are made to provide accurate fret spacing for the guitar’s intonation to be correct. The bridge is then built. Finishing products are then applied before being sanded and polished. Once cured all components are assembled and detailed work e.g. inlays and construction of the nut and saddle are completed before the tuners are installed and the guitar is strung up and ready to play.
How are acoustic guitars built?
Before we get too far into this guide. I want to point out I’m not a luthier. Luthiers are highly skilled craftsmen who do magical things with wood.
Consider the fact that an average guitar might weigh between 2 and 5lbs, but must be capable of handling up to (and in some cases beyond) 200lbs of tension from the strings. So, while I’ve been around guitars most of my life, luthiery is a different beast, it’s an art form and one I greatly respect.
With this in mind, the process below is not a tutorial by any means. It’s intended as an overview of the process. Hopefully, it provides a taste of what you might encounter if you decide to learn how to make your own acoustic guitar, or helps you learn more about, and appreciate, the guitar you currently play.
Keep in mind also, that guitars differ from body style to body style and brand to brand, and processes vary, based on the use of machinery, experience, and expertise. So, the information below is simply one way to go about building an acoustic guitar. Ok, with that out of the way, let’s discuss how acoustic guitars are built.
The Process
For a relatively simple instrument (simple, does not mean easy) the process of building an acoustic guitar is highly sophisticated and involves the following steps:
- Assembling the raw materials (e.g. tonewoods)
- Making or sourcing the mold
- Making the soundboard
- Book matching the top
- Marking out the soundhole and installing the rosette
- Planing and thicknessing the soundboard
- Bracing
- Making The back of the guitar
- Planing and thicknessing
- Bracing the back
- Making the sides
- Heat bending the sides
- Linings
- Constructing the neck
- Joining the neck and headstock
- Adding the truss rod
- Cutting the headstock shape
- Building the heel
- Shaping the neck
- Assembly
- Fixing the neck to the body
- Adding linings
- Installing the soundboard
- Installing the back
- Binding
- The Fretboard
- Fret positioning
- Installing the fret wires
- Making the bridge
- Finishing
- Installing the bridge
- Completing the build
As you might imagine, there’s a lot to cover in this article. We’ll get things underway with an overview of perhaps the most important component, assembling the raw materials, or tonewoods.
Assembling the raw materials
The guitar building process begins with the assembling of raw materials, aka tonewoods. When it comes to building an acoustic guitar this means selecting the wood for the body (soundboard, back, and sides), the neck, fretboard, and bridge.
Each component of the guitar plays a different role in how the guitar sounds and plays, and as a result, may utilize different materials and different species of timber that have different characteristics.
The soundboard
The most important component of the acoustic guitar is undoubtedly the soundboard or top wood. This is the component most responsible for the tone, responsiveness, and projection of the guitar and is usually constructed from a strong, yet light species of timber such as Spruce.
Spruce has also been used extensively in the design of aircraft due to its strength-to-weight ratio. Countless other materials are often also used including Mahogany, Cedar, and more exotic wood species such as Koa.
When you order wood for the soundboard and back of the guitar body from a luthier supplier the timber is first split and then cut into pairs. The pairs are generally matched, so they appear as a mirror-image of one another, this is known as book matching.
Tonewoods are graded based on their quality with regard to defects e.g. knots. A skilled luthier, if trying to create a specific sounding instrument, not only selects wood for each guitar based on its appearance, but also the acoustic properties of the wood.
Some luthiers can get a good idea of the acoustic properties of the wood by tapping on the wood (tone-tapping) and listening for the sound it makes. For tonewoods especially suited to acoustic guitar construction, the sound is often described, even in this raw state, as bell-like.
Back and Sides
The timber for the back will follow much the same process as the top but will often be of a different species of wood. The back and sides are usually paired and made up of a more rigid material, allowing the top greater resonance, much like the skin of a drum.
The wood for the sides is normally ordered as a prepared blank, consisting of two adjacent sections of wood that are also matched with regard to color and grain pattern. The most common wood species used for the back and sides are Rosewood, Mahogany, and Maple.
The Neck
The neck must be light enough for the guitar to feel balanced in the hands of the player, but also strong enough to maintain structural integrity under tension. If not, the intonation of the guitar (how in tune the guitar is with itself) and action (string height) will be affected negatively.
This is important over the lifetime of the guitar also, and as a result, guitar necks are usually made from hardwoods such as Mahogany and/or Maple which are known for their density and therefore structural integrity.
The Fretboard
The fretboard, aka fingerboard, must be durable enough to handle the steel strings being pushed down against it, not to mention the fingernails of the fretting hand. Ebony and Rosewood, along with Maple are the most common fretboard materials, with the majority of acoustic guitars featuring a Rosewood neck.
Rosewood is a particularly well-suited species of timber for this purpose as it is naturally oily, reducing friction between the guitarist’s fingers and the fretboard.
Ebony is similar, but darker in appearance and more sought after, but is often more expensive and takes considerably longer to dry.
Rosewood has become more difficult to acquire over the past few years due to regulations protecting it from over-harvesting. As a result, engineered Rosewood is now also commonly used.
Bracing (Struts)

The soundboard and back of the guitar are reinforced to retain their structure against the tension of the strings, this is known as bracing. The bracing pattern also disperses the vibrations passed on from the bridge throughout the body.
As the struts are attached directly to the underside of the soundboard and back of the guitar they must be sufficiently light, so as not to reduce the vibrational energy of the soundboard significantly, but also, like the soundboard, have sufficient strength to maintain its structure over the life-time of the guitar.
In many cases, the individual struts are made from the same species of timber as the soundboard and in some cases scalloped to reduce weight while maintaining strength. Scalloped bracing, refers to some of the material being removed e.g. scalloped to reduce the weight of the bracing.
The video below from Tony Polecastro, formerly of the Acoustic Letter YouTube channel, and now acousticlive.tv provides a great side-by-side comparison of scalloped V non-scalloped bracing.
Linings
If you consider the soundboard and the top and bottom edges of the sides of an acoustic guitar, there isn’t a great deal of space for the glue to be applied for joining the back and soundboard to the sides.
Because of this linings are used to increase the surface area so more glue can be applied. In many cases, the same materials used to construct the sides are also used for the linings.
Bindings
Bindings are the thin strips that separate the soundboard and the back and sides, and are sometimes used on the back of the guitar as well (double binding). While appearing mostly decorative, binding serves a couple of useful purposes.
For one binding protects the hard edges of the guitar which are most likely to be damaged by impact. Secondly, they shield the end grains of the soundboard from absorbing moisture.
Many necks are also bound. This can prevent fret ends from sticking out (fret sprout) on the edges of the neck, which can happen if the fretboard timber shrinks due to changes in humidity e.g. you purchased a guitar overseas, or from a more humid environment and the fretboard timber loses moisture when you bring it home.
Bindings are usually made from wood, plastic, or cellulose. Not all acoustic guitars feature binding.
Making or sourcing the mold
The mold is the template used for marking out the back and top of the guitar and bending the sides of the guitar body. Molds are made to specific body styles and sizes.
You can buy molds from luthier suppliers, or even sites such as Amazon and eBay, or many luthiers simply make their own.
Book matching
Book matching involves matching two sections of wood (your blanks for the soundboard) so that it appears the grains are mirror images of one another.
Once you have assembled the required materials the next step is to book match the soundboard of the guitar by aligning the wooden blanks so that the grain pattern aligns. The two sections are then glued together and laid out flat to prevent either side from moving or raising. Both edges must be dressed to allow contact across the entire length of the joint.
The two sections are then glued together under pressure to prevent any movement and then held in place to prevent any section of the wood from lifting. This can be done using clamps or tape.
Once this stage is complete the outside dimensions of the guitar body are marked by tracing the inside edges of the mold.
Marking out the soundhole and installing the rosette
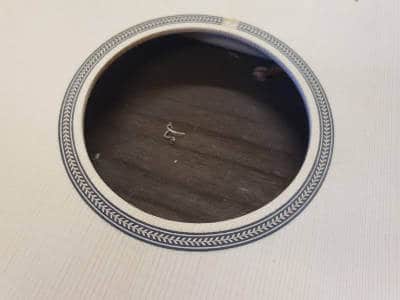
Placement of the soundhole is carefully planned and takes into account the diameter of the soundhole itself, the width of the rosette (the decorative element surrounding the soundhole), the guitar’s scale length (the length between the nut and saddle that the string can vibrate) and position where the guitar neck joins the body.
Luthiers may mark the entire soundboard on paper first to ensure the location of the soundhole is correct.
Drilling the center for the soundhole isn’t straightforward as this involves drilling through the glue line that joins the two sections of the soundboard and often requires a template so the drill is not moved off-center when encountering the glue.
Once the center is established the dimensions of the soundhole can be marked and the rosette can be placed and traced.
The rosette, much like binding, is not only decorative but also protects the edges of the soundhole. A channel is cut around the circumference of the soundhole and the rosette is placed within it to sit close, almost flush with the top of the soundboard (allowing sufficient excess for planing) using a circle cutting jig although some luthiers may perform this task using a chisel.
Planing and thicknessing the soundboard
Planing
Once the rosette is in place the soundboard can be planed.
The entire square soundboard can be planed, or the shape can be cut first before planing. In most cases, this isn’t a precise cut and mostly involves removing excess from the outside of the body while retaining much of the excess above the upper bout of the guitar body for handling the soundboard.
Thicknessing
The thickness of the soundboard must be consistent, this is critical to the sound of the guitar and requires the use of a thickness gauge, which must be used to check the thickness of the soundboard while planing.
The finished thickness varies based on the type of guitar being constructed, but in most cases will be within 1.5 to 2.5mm, depending on the tonewood selected for the top, with some graduation of thickness on the edges of the soundboard, particularly beneath the location of the soundhole.
Bracing
Once the soundboard is thicknessed bracing is installed.
This involves making the individual struts from softwood (often the same material used for the soundboard) and then gluing them in place on the underside of the soundboard to reinforce it when the guitar is played.
This allows the top to withstand the tension placed upon it by the strings and distributes the vibrations evenly throughout the body.
How the bracing is designed and how the individual struts create shapes within the soundboard determine how specific frequencies are handled by the guitar. For example, smaller more rigid areas will be more responsive to frequencies in the mid to upper ranges while larger, less rigid areas of the soundboard will respond to low-end frequencies.
The weight of the bracing system as a whole will also influence how responsive and resonant the guitar is and the overtones produced which form a large part of the guitar’s tone.
The bridge is also marked out at this stage as it also determines the placement of the bridge plate.
The video below demonstrates how different bracing patterns affect the tone of the guitar.
Classical guitars often utilize a system of bracing known as fan bracing, while steel-string acoustic guitars typically use X bracing, a stronger method of bracing to handle the added tension from steel guitar strings, as opposed to nylon.
In 2011 Taylor Guitars introduced V style bracing, which was considered revolutionary at the time. See if you can notice any difference by playing the video below.
Note, the soundhole is often cut at this point also.
As the channel removed for the installation of the rosette means the depth in that particular section of the soundboard is now quite thin, it is also reinforced using the same material as the soundboard on each side of the soundhole.
The Back of the Guitar
Planing and thicknessing
The process of joining the blanks and preparing the back of the guitar is similar to the front of the guitar with a couple of obvious exceptions.
For example, the back of the guitar will be of a hardwood species e.g. Rosewood or Mahogany most commonly, and there’s obviously no soundhole or rosette to consider.
The thickness of the back may differ from the soundboard depending on the materials used. Rosewood, for example, being a hardwood is a denser material than Spruce and needs to be reduced to just over 2mm approximately, so it isn’t adding unwanted weight to the body of the guitar. A less dense hardwood such as Mahogany might allow for an additional 1 – 1.5mm.
Bracing the back
The back also uses a different system of bracing as it doesn’t resonate to the same extent as the soundboard, this is referred to as ladder bracing as the support bars run horizontally across the body of the guitar like rungs on a ladder.
How the back is braced, to an extent at least, determines how much of a role the back of the guitar plays in the overall tonality of the guitar concerning frequency response.
If the back of the guitar is particularly ‘live’ e.g. it resonates more than a non-live back, it plays more of an active role in the tone of the guitar e.g. the overtones produced, but can also reduce the overall volume of the guitar.
Support bars are first installed on the inside of the back of the guitar at the widest point of both the upper and lower bouts, with another support between the two and another closer to the bottom of the guitar. They may be constructed from the same material as the soundboard or of the same material used for the back of the guitar.
A support bar running vertically along the joint is also installed. Ideally, the grain pattern of the vertical support bar will run at right angles to the grain pattern of the back of the guitar. This is known as crossbanding and reinforces the centerline of the two blanks which are now glued together.
Once this is completed the shape is usually cut, but a small area on each side of the waist or above the shoulders of the guitar is often retained to allow for handling.
Making the sides
The blanks used for the sides of the guitar are usually finished (e.g. planed) before being cut to shape. The thickness depends on the material used again, but in this instance, it has more to do with the side’s ability to bend to the shape of the guitar taking into account the upper and lower bout and waist.
If the sides are Rosewood, for example, the finished thickness might be somewhere in the vicinity of 1.5mm, whereas Mahogany can be thicker e.g. up to 2mm.
The sides must be precise.
The first task is to cut the sides at the correct length, which, being curved can be difficult to measure accurately. The simplest method to find the length is to measure the inside of the mold and then add an additional section e.g. 50mm for clamping.
The depth of the sides is the next consideration and as the sides are not uniform a template is used.
There’s no standard height used for the sides, as it largely depends on the body style of the guitar. For example my concert size steel-string acoustic guitar has a depth of 95mm at the bottom and 85mm at the neck pocket. This is much the same for modern classical guitars.
As a general rule the widest section (near the bottom of the guitar) on the most common body style, a dreadnought, will generally be close to 115 mm with the section closer to the neck joint being approx. 10 mm shallower.
It should be remembered this also takes into account the soundboard and back of the guitar, so the finished height of the sides must be reduced by the combined depth of both the top and back of the guitar.
Once marked, the sides are usually cut with a band saw or coping saw and then planed to a uniform finish.
Heat bending the sides

Bending the sides to the required shape requires heat. Bending irons, such as this one from Stewmac.com are commonly used, along with makeshift heat-bending tubes.
This requires experience, as it is easy to scorch the timber. In some cases, lighter timbers such as Maple may be soaked in water before heat-bending.
The heat is first applied to the waist of the guitar which is clearly marked. The wood is then slid back and forth across the heat to ensure a gradual curve.
This is followed by the same process for the upper and lower bouts before the sides are then placed into the mold and braced both vertically and horizontally to ensure the body shape is retained.
The sides should follow the inside dimensions of the mold with no visible gaps. The sides can be reheated to correct any areas where the sides are not in complete contact with the mold and once complete the excess 50mm discussed earlier for clamping can be removed.
Constructing the Neck
Joining the neck and headstock
The neck consists of the headstock and neck. Neck blanks are normally supplied at approx. 25mm thickness with the headstock height normally being finished at 17mm thick, while the neck itself will be of a similar depth, except for the end nearest the headstock which is usually 2-3mm shallower.
The two pieces are usually connected by a scarf joint, which is typically stronger than a single piece of wood. Single pieces are however often used as well, however a scarf joint results in less waste material as less excess needs to be removed. The video below demonstrates this concept.
The joint itself is defined by the neck angle, which is usually between 12 and 15 degrees on an acoustic guitar. Due to the angle of the cut, a large surface area remains to allow good surface contact for gluing the two individual pieces together.
Once the cut is made the headstock piece is reversed to allow the long grain on both the neck and headstock to be in contact with one another, and the headstock section is positioned beneath the angled cut of the neck to create the desired angle.
They are then glued and clamped into place. However, due to the large angle the two individual sections of timber are placed upon, there is the possibility that the position of the two pieces will slide, so the sections are often screwed into place with the screws being placed in a section that will be removed later e.g. the tuning peg holes, or in the case of a slotted headstock the area that will be removed to form the slots.
Lines are then marked to represent the position of the nut. This also indicates where the fretboard will begin when eventually installed on the neck.
Some manufacturers also utilize a veneer at this stage as a decorative element on the headstock.
Adding the truss rod
Once dry the neck and headstock and planed the truss rod cavity is routed and the truss rod is placed within the neck.
Truss rods are used to maintain neck stiffness and can be adjusted to counter either neck bow e.g. the neck is either flat or bends outward, or too much neck relief e.g. the neck bows inward, and the action, especially around the 12th fret of the neck is too high.
Shaping the headstock
Next, a line is drawn to mark the center of the headstock and neck, and the position of the tuners is marked and drilled. The headstock is then carefully shaped.
When performing any cutting e.g. cutting the shape of the body, or headstock the cut itself is made well outside of the lines to allow sufficient room for sanding to a smooth finish.
Building the heel
Next, the heel is created with excess material left over from the neck. These sections are sometimes cut and joined in layers, before being shaped and glued to the end of the neck to form the heel which connects the neck to the body of the guitar using a dovetail joint.
Shaping the neck
Once the heel is completed the neck is usually shaped. This is more difficult than it might first appear as the neck must have a continuous taper up to the position of the heel.
The neck itself, if worked on by hand, might be shaped using a spokeshave or similar tool. Once shaped the entire neck, including the headstock is roughly sanded.
Assembly
It’s at this point that the soundboard, back, sides, linings, and neck are completed, at least to a point where the assembly process can begin.
This usually involves firstly adding a tail block to the bottom of the sides of the guitar. The tail block serves a couple of purposes, firstly it allows a solid section of wood for the sides to be connected to, and secondly provides a solid piece of wood for the strap button to be installed within, without the risk of it becoming dislodged.
Fitting the neck
Next, the neck is fitted to the sides of the guitar. This must be precise, so center lines are marked and aligned.
The neck must also sit at the correct angle to allow for proper action and correct intonation.
The front section, where the sides meet, must be cut to fit the neck. The neck is then placed and sits just above the first crossbar on the underside of the back of the guitar.
A lot of planning goes into this stage of the guitar build to ensure the neck is perfectly aligned and the neck angle is correct. The neck is dry fit using clamps at this stage to ensure the placement of the neck is precise.
Adding linings
We discussed linings earlier when discussing assembling raw materials. Linings are used to increase the surface area between the sides and soundboard and back of the guitar, which would otherwise offer only a very small surface area for the glue to be applied.
However, the linings must be sufficiently light so as not to add additional weight to the soundboard which would affect its resonant capabilities. They must also be able to be installed on the inside curves of the guitar.
One way this is done is by taking a straight section of wood and cutting several cuts to a sufficient depth to allow the linings to bend to the interior shape of the guitar. This is known as a kerfed lining.
The fit of the linings is determined by the depth of the individual cuts and how closely spaced they are. Linings may then be bent into shape with heat in much the same way as the sides.
They are then glued into place, held in place by pegs or a similar holding device, and positioned near one another. The linings should sit proud of the sides to allow room for finishing flush with the sides.
Installing the soundboard and neck

Next, the top of the guitar is placed inside the mold. The neck and sides, which are now joined, are placed on top.
The struts from the bracing may need to be trimmed to fit within the linings, or the linings trimmed to allow for the struts, to ensure a perfect fit.
Dow, or similar material, is then used to press the sides against the inside edge of the mold to retain the shape of the body. They must be sufficiently tight to ensure the sides do not move, but the guitar must also be able to be removed from the mold easily.
Once in place, the top is glued utilizing the additional surface area the linings provide.
The end of the neck which is now sitting flush on the underside of the soundboard is also glued in place. It will sit flush with or very close to the first crossbar, if in direct contact this face is also often glued.
Installing the back
The back is installed next, but the heel must first be trimmed to sit comfortably within the first crossbar of the back of the guitar. Once done, the linings, and tail block must be finished flat to allow the back to sit flush with the sides of the guitar.
Once completed the back will sit in place on top of the sides, not flush, as the linings need to be cut in place to allow for the edges of the struts to fit within the lining, ensuring the back can then sit flush with the sides and make solid contact with the linings.
As per fitting the soundboard, a dry run is performed first to identify any potential problem areas, and once the luthier is satisfied the back is glued in place.
The minimum required glue is used at this point as it will be visible through the soundhole and obviously will be very difficult to remove or clean up once the back and soundboard are glued in place permanently.
Glue is applied to the heel and tail block, followed by the linings, and the back is installed.
The soundbox of the guitar should now be in place. It will still require finishing e.g. tidying up any excess but for the most part, is complete.
Binding
It’s at this stage that binding is installed to protect the edges of the guitar body. Binding can be purchased in either wood or plastic, or binding strips can be cut.
Bindings purchased from luthier suppliers may include purfling, which is the decorative inside layer of the binding often seen on high-end guitars.
Binding is typically between 3mm and 7mm deep and up to 3mm thick. To fit the binding the same amount of material (up to 3mm) must be removed from the soundboard, and sides adjacent to the top of the guitar (and the back and bottom of the sides if binding the bottom).
This is precision work, there should be no gaps between the binding and the sides and top of the guitar.
The dimensions are marked out using an adjustable inlay cutter or specialist binding cutter and cleaned out using a chisel. Or, a specialist tool such as a binding router is used, as seen here.
The binding is fitted next and is often heat bent first to take the form of the guitar body while reducing the possibility of cracks occurring from being more or less forced into place. Cracks in binding may be highly visible, depending on the materials used, so every precaution is taken to prevent cracks from occurring.
The Fretboard
The fretboard is typically installed next. Blanks are acquired and trimmed to the required width and height. In most cases, especially when building an acoustic guitar, the material used will be Rosewood, but Ebony is also very popular.
The luthier will typically inspect the fretboard and select its best side before finishing the surface to a smooth finish.
For classical guitars and some acoustic guitars, the fretboard will be flat. Most acoustic guitars however feature a small radius but not to the same extent as some electric guitars.
This ‘roundness’ of the fretboard is referred to as fretboard radius e.g. a guitar may feature a radiused fretboard designed to suit the natural curvature of our hands.
The fretboard tapers between the nut and the neck pocket. The nut width might be somewhere in the vicinity of 42 – 46mm, although there are exceptions. While the width (where the fretboard connects to the body) may be up to 20mm wider.
The nut width is often dependent on the design of the guitar and how the guitar is intended to be played. For example, a wider nut width allows for a wider string spacing and is ideal for fingerstyle guitars.
Classical guitars, which are always played with the fingers often feature a much wider nut width than a dreadnought guitar which is more accustomed to being strummed using a pick.
Once the fretboard is dressed and ready for installation it is positioned carefully in place and glued in place on the neck. Once dry any excess material is trimmed so the fretboard is perfectly flush with the neck.
Fret positioning
Fret placement, and fret wire positioning is performed next. This is also quite complex, and requires an understanding of scale length, the number of frets the guitar will have (most acoustic guitars have 20 frets, while classical guitars often feature 19 frets), and how music essentially works with regard to the vibrating length of the strings. For example, if we reduce the length of the string that can freely vibrate by fretting a note, the pitch is raised, relative to the fret being played.
In one sense, you might think this would therefore require 12 equally spaced frets per octave but it doesn’t work this way.
Frets are spaced logarithmically so that each additional fret shortens the length of the strings equal to the same proportions as the fret before it.
Fret position calculators can be used, such as this one from Stewmac.com
Keep in mind also, that the strings do not lie flush against the fretboard and must be pressed onto the fretboard when fretted, which increases the tension on the string. This must be compensated e.g. the 12th fret should not be exactly half the length of the neck, as the 12th fret would sound sharp if it doesn’t take into account the additional tension placed on the string when fretted.
As a rule, the thicker the string the more compensation is required.
This compensation is performed at the bridge and is why you will often see the saddle placed at an angle within the bridge. Along with this measure being taken, compensated saddles are also commonly seen on acoustic guitars. This is also why changing a right-handed guitar to a left-handed or vice versa involves more than simply switching over the strings.
A compensated saddle is normally thicker than a standard saddle and has space removed at the back or front of the saddle aligning with specific strings of the guitar, to reduce the width of the exact point of contact of the strings. This pushes the contact point closer to the nut or further from the nut. This is often just a few mm.

This is less essential on nylon string guitars, although it is still used, only to a lesser degree as the tension placed on nylon strings as opposed to steel strings is considerably less.
Once the individual frets are marked the grooves for the fret wires are sawn. The frets must be sawn vertically and must be perfectly straight.
Fret saws are designed for this purpose. The width of the cut is important also e.g. It should be neither too narrow nor too wide. If too narrow the fret wires will need to be placed with too much force, or the fret wires will be too loose.
This often means the fret slots must be cut in one action of the saw. Repeated cuts will only widen the groove causing problems when it comes time to fit the individual fret wires.
The depth of the cut is determined by the tang, which refers to the depth of the fret wires.
Installing the fret wires
Fret wires come most commonly in a large roll and are available in a variety of heights and shapes. Larger (higher) fret wires however are becoming ever more popular as there is a perceived advantage in terms of the ability they provide for playing cleanly.
As the height of the frets increases so does the compensation at the bridge to allow for the greater tension involved in pushing the strings down against the fretboard.
Fret wires also come in different materials, with some being more durable while others are quite soft. There is a trade-off between the two, with softer frets generally accepted as being easier to play but also tend to wear out much faster.
Fret wires are installed using a fret hammer and trimmed using wire cutters. The neck should be resting on a support block with padding to protect the underside of the neck from being marked or dented.
Once hammered into place the wires are trimmed using the wire cutters and each fret wire is checked to ensure there are no spaces between the grooves and the fret wires.
Once the frets are installed the rough edges on each side of the neck are filed to appear flush to the edge of the neck. The top half of the fret wires are filed on an angle of approx. 10 degrees to create a chamfer.
The bridge
If the soundboard is the component of the acoustic guitar most responsible for volume and tone, the bridge is a close second. The vibrations from the strings are transferred via the bridge to the soundboard, so the bridge plays an essential role in how the acoustic guitar projects sound.
It’s also home to the string ball ends and saddle. It is also the only component that is attached to the top of the soundboard, so the weight of the bridge affects the resonant capabilities of the soundboard itself.
The bridge is usually manufactured from the same material as the fretboard e.g. Rosewood, or Ebony, which also suits the aesthetics of the guitar.
Once the bridge is shaped, holes are drilled for the strings and the space the saddle will eventually sit within is routed to approx 5mm depth, taking into account compensation to allow accurate intonation.
The location of the bridge must be precise to ensure the scale length is correct. The location of the bridge is marked on the soundboard and the bridge is then placed in position with masking tape and the edges marked. Note the bridge is not installed at this point as the guitar is yet to be finished e.g. sanded and lacquered.
Finishing

It is usually at this point that all excess is trimmed and removed, and the surface prepared for finishing. This involves sanding the entire body and neck and masking any areas such as the fretboard that should not be exposed to finishing products.
An extensive overview of finishing is beyond the scope of this article as there are many different ways to finish a guitar (french polishing, spray finishing, or applying lacquer with a brush to name but a few).
But as a general rule, the process involves sanding the guitar to a smooth finish, working your way down from a medium grit paper e.g. 400 grit paper. Cleaning and conditioning the body and then applying the lacquer finish.
Some guitars feature a graduating color combination e.g. sunburst, others are stained and some acoustics are even painted a solid color, although the impact that has on the acoustics of the wood e.g. deadening the sound is often debated, personally, it’s not something I would do.
Once the lacquer has been applied the guitar is sanded to a very smooth finish using fine-grit sandpaper e.g. wet and dry 1500 grit. You may need to source this from an automotive store if you can’t find sandpaper of this grade in your local hardware store.
Finally, the guitar is usually buffed and polished.
Installing the Bridge
The marking made earlier for the bridge will still be visible through the now finished surface of the guitar and it is at this stage the bridge is usually fitted.
Luthiers will often utilize tack sheets at this point to preserve the finish of the guitar. The bridge is placed in position and the tack sheet is carefully marked and cut using a scalpel or similar tool. This is precise work as the soundboard cannot be marked.
Once complete the bridge is glued in place and clamped. However, as you might imagine this is difficult as the clamp must be fixed to the soundhole and extend outward to hold the bridge firmly in place. Specialist tools also exist for this purpose, although many luthiers simply create their own.
Finishing the Build
Once the bridge is installed the guitar is capable of being strung up and played. First, the tuning machines are installed so the guitar can be strung up and inlay work completed.
Classical guitars and some acoustic guitars don’t feature inlays and instead only have string position markers on the edges of the top side of the neck.
The frets are also dressed at this stage, which involves ensuring the tops of the frets are level to reduce the potential for fret buzz occurring and polished so strings slide easily over the top of them.
This usually involves masking the fretboard and using a combination of fret files, crowning tools, and abrasives to level, crown, and polish the frets.

The nut and saddle are either sourced independently or constructed next which in the case of the nut involves shaping and creating the nut slots for the strings to pass through.
The depth for each slot should be determined based on the depth of the strings e.g. the slot for the high E string is shallower than the slot for the low E string in comparison to the fretboard.
Once this step is completed, the guitar is more or less complete.
Summary
I hope the information above gives some insight into how acoustic guitars are built. As you can see, there are a lot of steps involved and each step requires expertise and precision to build a high-quality instrument.
In the case of acoustic guitars, and acoustic stringed instruments in general, the construction and materials used have a massive influence on the character of the instrument and are therefore carefully selected and assembled following the original intention of the luthier with regard to tonality, playability, and appearance.
If you have ever pictured yourself building an acoustic guitar, I strongly recommend you learn from an expert, by taking a guitar building course, there are a number of them available as some boutique luthiers look to increase their earning capacity through teaching.
Many of these are done in person, or there are options available online in the form of courses and dedicated books. In much the same way as learning to play guitar from a pre-recorded video, you won’t receive feedback on your work, and in many cases, it becomes far more difficult to ask questions.
Some include a community of similar-minded people you can request feedback from or ask questions. And, in the absence of an in-person guitar building class in your local area may make a good alternative.
Acoustic guitar kits are also available, such as this one from Amazon.com, although there are mixed reviews. The benefit of an acoustic guitar kit is much of the specialist work e.g. fretwork, inlay work, and heat bending (the sides of the guitar) are already completed and may make a good initial starting point.
Whichever way you choose to proceed, keep in mind there’s a lot to how acoustic guitars are made. I hope the information above helps explain the process or at least gives you an appreciation of the work that has gone into the acoustic guitar you are currently playing.
If you enjoyed this, my article on how the acoustic guitar works is a good companion article that will explain some of the methods described above in even greater detail.